The orange light on your Carrier furnace indicates potential issues that could impact performance and safety. It often points to dirty burners, improper gas flow, or ignition system problems. If you see this light, start by checking the air filter and inspecting the ignition system. Sometimes, it might stem from blocked vents or faulty thermostats. Ignoring the light can lead to reduced heat and safety risks, like gas leaks. Regular maintenance and visual inspections can help catch issues early. If the light persists after troubleshooting, uncover further steps to resolve the problem effectively.
Key Takeaways
- The orange light on a Carrier furnace signals potential issues affecting performance and safety, such as dirty burners or gas flow problems.
- Common causes for the orange light include faulty ignition systems, blocked vents, and airflow issues from clogged filters.
- Regular visual inspections and burner cleanings can help identify and resolve problems indicated by the orange light.
- Consult the user manual or a professional if the orange light persists after performing basic troubleshooting steps.
- Ignoring the orange light may lead to reduced heat output and safety hazards, including gas leaks.
Understanding the Orange Light

When you see an orange light on your Carrier furnace, it's important to understand what it means for your heating system. This light often indicates a problem that could affect performance or safety. Common causes include dirty burners, incorrect gas flow, or issues with the gas supply line. It might also signal an ignition system malfunction or a faulty flame sensor. Ignoring the orange light can lead to reduced heat production and potential safety hazards, including gas leaks. To address this, start with a visual inspection and clean the burners if necessary. If the light persists, it's advisable to consult your user manual or seek professional help to guarantee your furnace operates safely and efficiently. Additionally, be aware that a continuous flashing light can indicate power issues or component failures.
Common Issues Explained

Understanding common issues with your Carrier furnace is vital for maintaining its efficiency and safety.
Airflow problems often stem from clogged filters, blocked vents, or ductwork issues. Verify your thermostat settings are correct and replace air filters regularly. Regular maintenance can prevent yellow light codes that indicate malfunctions in the system.
Ignition system issues can arise from a faulty igniter, pilot light problems, or gas valve issues. A dirty flame sensor or low gas pressure can also disrupt ignition.
Blower motor failures may result from overload, electrical issues, or clogged filters, so regular maintenance is key.
Thermostat malfunctions can often be fixed by checking settings, replacing batteries, or recalibrating.
Finally, be aware of heat exchanger issues, as cracks can lead to serious safety hazards. Regular inspections are vital for preventing these problems.
Diagnostic Steps to Follow
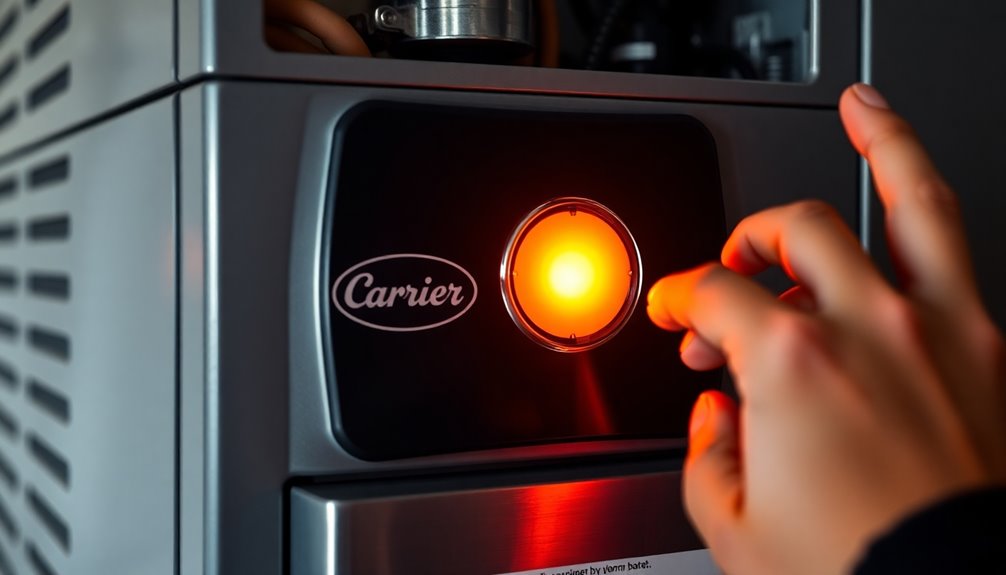
Troubleshooting your Carrier furnace can feel overwhelming, but following systematic diagnostic steps simplifies the process.
First, verify the power source by checking the breaker and confirm your thermostat is functioning properly; test its calibration and reset it if needed.
Next, inspect the air filter—clean or replace it to maintain airflow and check for any obstructions in the vent. Regularly replacing or cleaning air filters ensures proper airflow and can prevent overheating issues.
Then, examine the ignition system; look for wear on the igniter and confirm the pilot light is activated.
Finally, evaluate electrical connections. Check that they're properly oriented and use a multimeter to test them.
If you encounter persistent issues, don't hesitate to seek professional assistance. Following these steps can help you identify and resolve problems effectively.
Carrier Furnace Error Codes

Carrier furnace error codes provide essential insights into the system's performance, helping you quickly identify issues that may arise. Your furnace may display alphanumeric codes, like "33" or "13," or use blinking LED lights to indicate specific errors. For instance, Error Code 1-1 shows no previous code, while 1-2 indicates the blower's operation after power-up. If you see Error Code 1-3, it means there's a lockout due to the limit or flame roll-out switch. Error Code 2-1 signals a gas heating lockout that requires inspection of your gas valve. Understanding these codes and their implications can be crucial for addressing common causes of lockouts. Knowing these codes can save you time and help you determine the right solutions for your Carrier furnace's performance issues.
Troubleshooting Tips
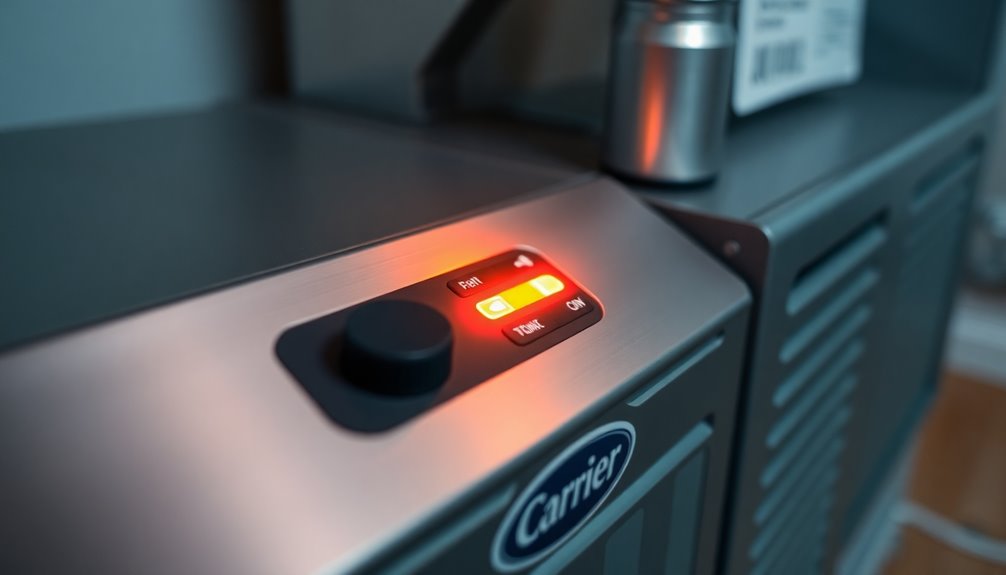
When your Carrier furnace displays error codes, it's important to act quickly to restore comfort in your home.
Start by checking your thermostat settings. Make sure it's set to "heat" mode and the desired temperature. If needed, replace the batteries.
Next, inspect the air filter; if it's dirty or clogged, replace it to guarantee proper airflow. Regular filter checks can prevent airflow restrictions and improve overall efficiency.
Check for electrical issues by confirming connections are secure and that the circuit breaker isn't tripped.
Address any blower motor problems by verifying its speed and calibration.
Finally, identify gas valve issues; verify it's functioning correctly and that there's no obstruction in the gas supply line.
If you're uncertain about any steps, don't hesitate to call a professional for help.
Preventive Maintenance Measures

To keep your furnace running efficiently and avoid costly repairs, regular preventive maintenance is crucial.
Start by changing or cleaning your air filter every 1 to 3 months and check its condition monthly. Make sure you use compatible filters and replace disposable ones at least twice a year.
Next, calibrate your thermostat for accurate temperature readings and check the battery if it's battery-powered. Regularly checking your thermostat settings can optimize temperature settings for better efficiency.
Schedule an annual inspection with a qualified HVAC technician to conduct an extensive review of your furnace, including a heat exchanger inspection.
Additionally, lubricate furnace parts annually, using the recommended lubricant, and clean the blower assembly and interior components.
Finally, verify that the flue and venting system are clear to guarantee safe operation. Regular professional maintenance can help identify hidden issues that may affect performance.
When to Seek Professional Help

If you're facing persistent issues with your furnace, knowing when to call in a professional can save you time and money.
If you encounter complex error codes that you can't resolve, don't hesitate to reach out for help. Repeated codes often signal deeper problems best handled by experts.
Additionally, if you notice any gas leaks or irregular gas flow, call a technician immediately—these are serious safety hazards. Regular maintenance can also help prevent some of these issues from arising in the first place.
Electrical issues, especially those related to wiring or microprocessors, also require professional intervention for safety and accurate diagnosis.
Using specialized tools, professionals can effectively address these intricate issues, ensuring your furnace operates safely and efficiently.
Prioritizing safety means knowing when to let the experts take over.
Frequently Asked Questions
Can I Reset the Furnace After Seeing the Orange Light?
You can try resetting your furnace after seeing the orange light, but it's not always a straightforward fix. Typically, this light indicates an issue that might require professional attention.
If you reset it, be cautious and follow the manufacturer's instructions. However, if the problem persists, it's best to consult a technician.
They can guarantee everything's working safely and prevent potential hazards, like carbon monoxide buildup, from occurring.
How Long Does It Take to Clean the Burners?
Cleaning the burners takes about 45 to 60 minutes.
You'll start by removing access doors and burner covers, which takes roughly 15-25 minutes.
Then, vacuuming the burners can add another 20-30 minutes.
After that, you'll spend about 15 minutes cleaning the burner channels, followed by 10-15 minutes on final inspection and maintenance.
Overall, it's a straightforward process that guarantees your furnace runs efficiently.
Don't rush; thoroughness is key!
What Tools Do I Need for Furnace Maintenance?
For furnace maintenance, you'll need a few essential tools.
Grab a utility knife for cutting insulation, an adjustable wrench for various fittings, and a cordless drill for driving screws.
An inspection mirror helps you see hard-to-reach areas, while a digital thermometer guarantees accurate temperature readings.
Don't forget a filter puller for easy filter changes and a service wrench for refrigeration valves.
These tools will make your maintenance tasks smoother and more efficient!
Is the Orange Light an Emergency Situation?
No, the orange light isn't an emergency situation. It signals a potential issue, often due to dirt build-up affecting gas supply and heating efficiency.
While it's not critical, it's important you address it promptly to avoid worsening problems. Check your burners and clean them if necessary.
If you're unsure or the light persists, don't hesitate to contact a professional technician for help. Regular maintenance can also prevent such issues in the future.
Can I Perform Repairs Myself Safely?
Yes, you can perform repairs on your Carrier furnace safely, but you need to take precautions.
Start by turning off the power and gas supply. Use the right tools and wear protective gear like gloves and safety glasses.
Always consult the manual for guidance and check for hazards like gas leaks or electrical risks.
If you feel uncertain about any step, it's best to call a professional to avoid potential dangers.
Conclusion
In summary, understanding the orange light on your Carrier furnace is key to keeping it running smoothly. By recognizing the common issues and following the diagnostic steps outlined, you can often troubleshoot the problem yourself. Remember to stay proactive with preventive maintenance to avoid future issues. If you're ever unsure or the problem persists, don't hesitate to seek professional help. Keeping your furnace in top shape guarantees a warm and comfortable home all season long!